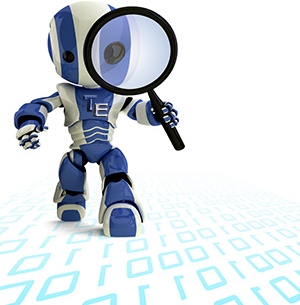
Testability can best be described as the ease with which the functionality of any electronic product circuit or component can be determined to a desired degree of accuracy. To put it more simply, how easily can it be checked for performance to-spec throughout the entire product life cycle from product concept through design, manufacture, and service? How quickly can test programs be generated? How accessible are the test points? How comprehensive is the fault coverage?